Je nach Anwendungsbereich und Ausgangsmaterial werden bei autogena stahl die Brennschneidverfahren autogenes Brennschneiden und Plasmaschneiden zur Herstellung der Brennzuschnitte eingesetzt.
Autogenes Brennschneiden von Stahl
Das autogene Brennschneiden oder Autogenschneiden von Stahl zeichnet sich durch eine hohe Brennschneidgüte auch bei großen Blechstärken aus. Mit einem Brenngas-Sauerstoff-Gemisch wird das Material lokal bis zur Zündtemperatur erwärmt und anschließend durch Zuschaltung eines Schneidsauerstoffstrahls verbrannt und ausgetrieben. Als Brenngas dient hier in der Regel Propan. Mit dem Bewegen des Schneidkopfes der Autogen-Brennschneidmaschine parallel zur Blechoberfläche entsteht eine Brennfuge, der sogenannte Brennschnitt.
CNC Brennschneiden
Bei der Firma autogena stahl GmbH sind alle Brennschneidmaschinen CNC-gesteuert. Das heißt im Rahmen der physikalischen Grenzen der Brennschneidtechnik können beliebige 2D-Konturen aus einem Blech herausgeschnitten werden. Hierzu verwenden wir Ihre Bauteilzeichnung und bereiten diese in unserem technischen Büro für die Brennmaschinen auf. Je nach Blechdicke und Kontur werden hier die Schnittbahn und die Schneidparameter für die Brennschneidmaschinen vorgegeben. Die Brennmaschine setzt diese Vorgaben dann unter Aufsicht und Feinjustierung unserer Fachkräfte an den Maschinen um.
Durch die Verwendung mehrerer Schneidköpfe gleichzeitig in einer Maschine können wir in der Serienfertigung eine entsprechende Anzahl gleichförmiger Teile zeitgleich herstellen, wobei wir mit bis zu 9 Schneidköpfen synchron arbeiten. Diese Brennschneidtechnik gewährleistet neben zuverlässiger Präzision und Vermeidung von Fehlern beim Brennschneiden vor allem auch Wirtschaftlichkeit, die sich für Sie im Preis der Zuschnitte niederschlägt.
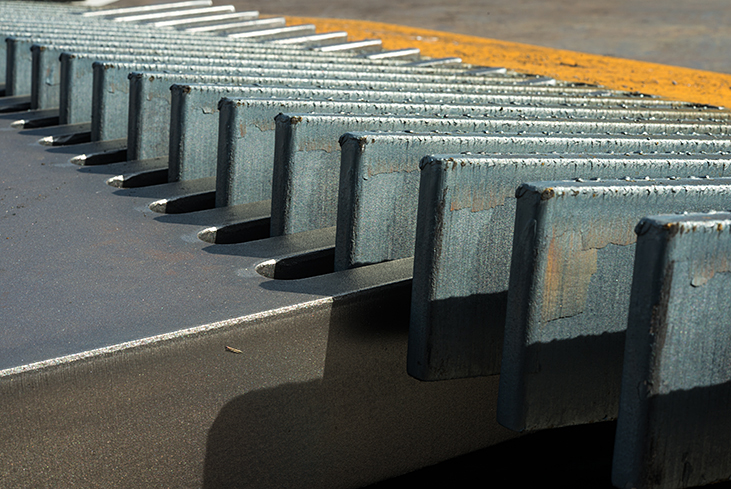
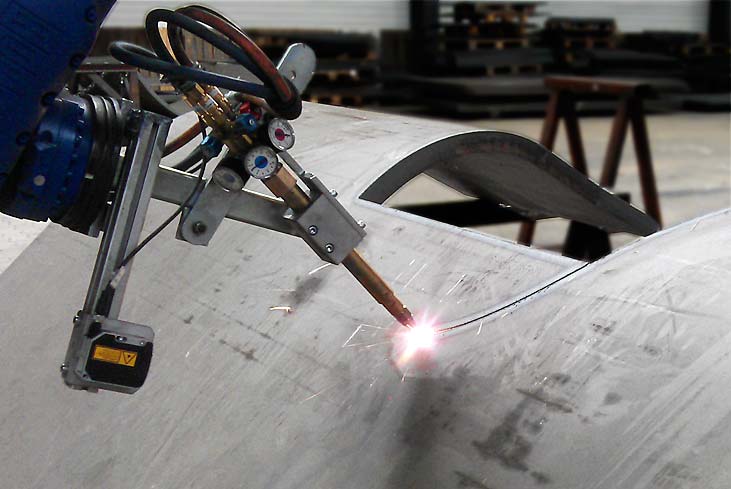
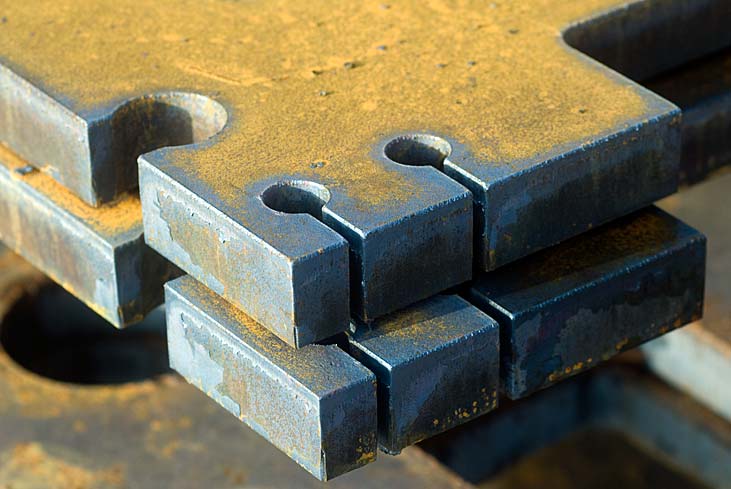
Plasmaschneiden Stahl
Mit dem Plasmaschneiden erzielen wir eine sehr gute Brennschneidgüte bei mittleren Blechstärken und hoher Schneidgeschwindigkeit. Das im Schneidkopf erzeugte, bis zu 30.000 °C heiße Plasma wird durch die Schneiddüse in Richtung der Blechoberfläche geführt. Dort wird das Material aufgeschmolzen und mit Luftdruck ausgetrieben. Prozesstechnisch ist die Plasmaschnittfuge V-förmig. Da die Plasma-Brennschneidmaschine bei autogena mit frei schwenkbaren Schneidköpfen arbeitet, sind wir in der Lage, diese normalerweise auftretende beidseitige Schräge im Schnitt so weit ausgleichen, dass das Gutteil nahezu einen 90-Grad-Winkel an der Schnittfläche hat. Das erleichtert Ihnen die saubere Weiterverarbeitung der Brennteile nach dem Plasma-Brennschneiden.

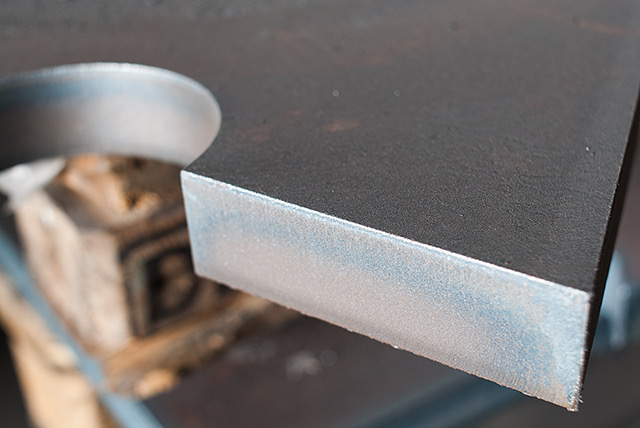
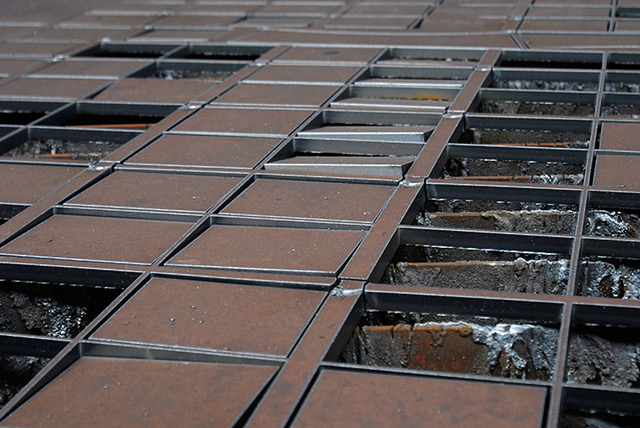
Rautiefe und Toleranzen Brennschneiden
Nicht nur in technischer, sondern auch in maßlicher Hinsicht erfüllen wir die höchsten Ansprüche. Die Brennschneidtoleranzen für unsere Verfahren sind in der Norm DIN EN ISO 9013 hinterlegt. Üblicherweise wird die Brennschnittqualität durch die Angabe der Norm und eine nachstehende Zahlenfolge definiert, als Beispiel: ISO 9013-342.
Hierbei bedeuten die Zahlen Folgendes:
1. Zahl: Rechtwinkligkeits- oder Neigungstoleranz (5 Klassen)
2. Zahl: gemittelte Rautiefe Rz5 (4 Klassen)
3. Zahl: Maßtoleranzen (2 Klassen)
Die entsprechenden Tabellen finden Sie hier:
Bereich | Rechtwinkligkeits- oder Neigungstoleranz, u (mm) |
1 | 0,05 + 0,003ɑ |
2 | 0,15 + 0,007ɑ |
3 | 0,4 + 0,01ɑ |
4 | 0,8 + 0,02ɑ |
5 | 1,2 + 0,035ɑ |
Bereich | Gemittelte Rautiefe RZ5 (µm) |
1 | 10 + (0,6ɑ:mm) |
2 | 40 + (0,8ɑ:mm) |
3 | 70 + (1,2ɑ:mm) |
4 | 110 + (1,8ɑ:mm) |
Maße in mm
Werkstückdicke | Nennmaße | |||||||||
> 0 < 3 | ≥ 3 < 10 | ≥ 10 < 35 | ≥ 35 < 125 | ≥ 125 < 315 | ≥ 315 < 1.000 | ≥ 1.000 < 2.000 | ≥ 2.000 < 4.000 | ≥ 4.000 < 6.000 | ≥ 6.000 < 8.000 |
|
Grenzabmaße | ||||||||||
> 0 ≤ 1 | ± 0,075 | ± 0,1 | ± 0,1 | ± 0,2 | ± 0,2 | ± 0,3 | ± 0,4 | ± 0,65 | ± 0,9 | ± 1,6 |
> 1 ≤ 3,15 | ± 0,1 | ± 0,15 | ± 0,2 | ± 0,25 | ± 0,25 | ± 0,35 | ± 0,4 | ± 0,65 | ± 1 | ± 1,75 |
> 3,15 ≤ 6,3 | ± 0,2 | ± 0,2 | ± 0,25 | ± 0,25 | ± 0,3 | ± 0,4 | ± 0,45 | ± 0,7 | ± 1,1 | ± 1,9 |
> 6,3 ≤ 10 | – | ± 0,25 | ± 0,3 | ± 0,3 | ± 0,35 | ± 0,45 | ± 0,55 | ±0,75 | ± 1,25 | ± 2,2 |
> 10 ≤ 15 | – | ± 0,3 | ± 0,35 | ± 0,4 | ± 0,45 | ± 0,55 | ± 0,65 | ± 0,85 | ± 1,5 | ± 2,5 |
> 15 ≤ 20 | – | ± 0,4 | ± 0,4 | ± 0,45 | ± 0,55 | ± 0,75 | ± 0,85 | ± 1,2 | ± 1,9 | ± 2,8 |
> 20 ≤ 25 | – | ± 0,45 | ± 0,5 | ± 0,6 | ± 0,7 | ± 0,9 | ± 1,1 | ± 1,6 | ± 2,4 | ± 3,25 |
> 25 ≤ 32 | – | – | ± 0,7 | ± 0,7 | ± 0,8 | ± 1 | ± 1,6 | ± 2,25 | ± 3 | ± 4 |
> 32 ≤ 50 | – | – | ± 0,7 | ± 0,7 | ± 0,8 | ± 1 | ± 1,6 | ± 2,5 | ± 3,8 | ± 5 |
> 50 ≤ 100 | – | – | ± 1,3 | ± 1,3 | ± 1,4 | ± 1,7 | ± 2,2 | ± 3,1 | ± 4,4 | ± 5,6 |
> 100 ≤ 150 | – | – | ± 1,9 | ± 2 | ± 2,1 | ± 2,3 | ± 2,9 | ± 3,8 | ± 5,1 | ± 6,3 |
> 150 ≤ 200 | – | – | ± 2,6 | ± 2,7 | ± 2,7 | ± 3 | ± 3,6 | ± 4,5 | ± 5,7 | ± 7 |
> 200 ≤ 250 | – | – | – | – | – | ± 3,7 | ± 4,2 | ± 5,2 | ± 6,4 | ± 7,7 |
> 250 ≤ 300 | – | – | – | – | – | ± 4,4 | ± 4,9 | ± 5,9 | ± 7,1 | ± 8,4 |
Maße in mm
Werkstückdicke | Nennmaße | |||||||||
> 0 < 3 | ≥ 3 < 10 | ≥ 10 < 35 | ≥ 35 < 125 | ≥ 125 < 315 | ≥ 315 < 1.000 | ≥ 1.000 < 2.000 | ≥ 2.000 < 4.000 | ≥ 4.000 < 6.000 | ≥ 6.000 < 8.000 |
|
Grenzabmaße | ||||||||||
> 0 ≤ 1 | ± 0,5 | ± 0,6 | ± 0,6 | ± 0,7 | ± 0,7 | ± 0,8 | ± 0,9 | ± 0,9 | – | – |
> 1 ≤ 3,15 | ± 0,6 | ± 0,6 | ± 0,7 | ± 0,7 | ± 0,8 | ± 0,9 | ± 1 | ± 1,1 | ± 1,4 | ± 1,4 |
> 3,15 ≤ 6,3 | ± 0,7 | ± 0,8 | ± 0,9 | ± 0,9 | ± 1,1 | ± 1,2 | ± 1,3 | ± 1,3 | ± 1,6 | ± 1,6 |
> 6,3 ≤ 10 | – | ± 1 | ± 1,1 | ± 1,3 | ± 1,4 | ± 1,5 | ± 1,6 | ± 1,7 | ± 1,9 | ± 2 |
> 10 ≤ 15 | – | ± 1,8 | ± 1,8 | ± 1,8 | ± 1,9 | ± 2,3 | ± 3 | ± 4,2 | ± 4,3 | ± 4,5 |
> 15 ≤ 20 | – | ± 1,8 | ± 1,8 | ± 1,8 | ± 1,9 | ± 2,3 | ± 3 | ± 4,2 | ± 4,3 | ± 4,5 |
> 20 ≤ 25 | – | ± 1,8 | ± 1,8 | ± 1,8 | ± 1,9 | ± 2,3 | ± 3 | ± 4,2 | ± 4,3 | ± 4,5 |
> 25 ≤ 32 | – | ± 1,8 | ± 1,8 | ± 1,8 | ± 1,9 | ± 2,3 | ± 3 | ± 4,2 | ± 4,3 | ± 4,5 |
> 32 ≤ 50 | – | ± 1,8 | ± 1,8 | ± 1,8 | ± 1,9 | ± 2,3 | ± 3 | ± 4,2 | ± 4,3 | ± 4,5 |
> 50 ≤ 100 | – | – | ± 2,5 | ± 2,5 | ± 2,6 | ± 3 | ± 3,7 | ± 4,9 | ± 5,3 | ± 5,6 |
> 100 ≤ 150 | – | – | ± 3,2 | ± 3,3 | ± 3,4 | ± 3,7 | ± 4,4 | ± 5,7 | ± 6,1 | ± 6,4 |
> 150 ≤ 200 | – | – | ± 4 | ± 4 | ± 4,1 | ± 4,5 | ± 5,2 | ± 6,4 | ± 6,8 | ± 7,1 |
> 200 ≤ 250 | – | – | – | – | – | ± 5,2 | ± 5,9 | ± 7,2 | ± 7,6 | ± 7,9 |
> 250 ≤ 300 | – | – | – | – | – | ± 6 | ± 6,7 | ± 7,9 | ± 8,3 | ± 8,6 |
CNC Brennschneiden Maschinenpark
Von Anfang an haben wir auf modernste Maschinentechnik und prozessoptimierte Fertigungsabläufe geachtet. Wir investieren kontinuierlich in die Modernisierung unseres Maschinenparks und passen die Fertigungsabläufe an die aktuellen Kundenanforderungen an. So wurden beispielsweise die Brenntische für autogenes Brennschneiden und Plasmaschneiden nochmals vergrößert, Anarbeitungsaggregate implementiert und kontinuierlich neue Brennmaschinen erworben.
- CNC-gesteuerte Autogenanlagen SATO HD 8500
- CNC-gesteuerte Autogenanlage Messer Omnimat 11000
- CNC-gesteuerte Plasmaanlagen Messer Multitherm mit Fasaggregat
Unsere maximale Dicke beim Brennschneiden beträgt aktuell 350 mm. Weitere Werte entnehmen Sie bitte der nachfolgenden Auflistung.
Brenntische
Autogen
- 11.000 x 50.000 mm
Plasma
- 5.000 x 42.000 mm
Brenndicken
Autogen
- 10 – 350 mm
Plasma
- 5 – 40 mm
Stückgewichte
bis zu 32 t
Blechlänge
bis zu 18.000 mm
Werkstoffe und Formate
Material | Norm | Modell | max. Dicke | max. Breite |
---|---|---|---|---|
Unlegierte Baustähle | EN 10025 | S235JR+N S235J2+N S355JR S355J2+N S355J2+N DBS S355K2+N S355NL S460 S690QL | 350 mm | 4.000 mm |
Druckbehälterstähle auch nach ASME/ASTM-Standard | EN 10028 | P265GH P275NL P295GH P355GH P355NL P460NL SA 516 Grad 60 SA 516 Grad 70 16Mo3 | 300 mm | 4.000 mm |
Schiffbaustähle | – | Grad A D36 E36 F36 | 250 mm | 4.000 mm |
Verschleißgüten | – | C45 400HB 500HB | 250 mm | 4.000 mm |
Abnahmeprüfungen der Brennteile
Notwendige Abnahmeprüfungen und die Übertragung der Stempelungen können wir direkt bei autogena durchführen lassen. Die Prüfungen werden von allen gängigen Prüfinstituten und Klassifikationsgesellschaften wie ABS, BV, DNV GL, LRS, RINA oder RS vorgenommen. Dabei ist das Umstempeln für die Rückverfolgbarkeit von 3.1 und 3.2 zertifiziertem Material inklusive der Vorhaltung der entsprechenden Zertifikate durch die Klassifikationsgesellschaften für uns eine Selbstverständlichkeit.
Weitere Aufgaben wie:
- Ultraschallprüfungen
- Oberflächenrissprüfungen
- Zugprüfungen in Dickenrichtung
- Härteprüfung
- Zusatzanalysen
- Aufschweißbiegeversuche
werden durch unabhängige Abnahmebeauftragten mehrfach pro Woche bei autogena stahl direkt oder in nachgeschalteten Prüflaboren durchgeführt. Dadurch findet die Zertifizierung Ihrer Sonderanforderungen direkt im Rahmen der Auftragsausführung statt. Das bedeutet keinen großen Zeitverlust und wirtschaftliche Fertigung nach höchsten Qualitätsansprüchen.
Bohrungen in den Brennteilen
Wir bereiten Ihre Brennteile mit Bohrungen und Gewinden exakt nach Ihren Anforderungen vor – bis 4.500 mm Länge und 1.000 mm Breite. Die komplette Bearbeitung erfolgt in unserem Werk, wodurch unnötige Wege entfallen. Das bedeutet für Sie: weniger Aufwand, geringere Kosten und ein verlässlicher Partner, der Ihre Prozesse unterstützt. Näheres erfahren Sie hier: Bohren
Entzundern und Entgraten
Beim Brennschneiden ist das Entzundern ein Prozess, bei dem die Oberfläche des Metalls von Oxid- und Schmelzrückständen befreit wird, die beim Schneiden entstehen. Diese Rückstände können die Qualität des Schnitts beeinträchtigen und die Haftung von Schweißnähten oder anderen Verbindungen beeinträchtigen. Durch das Entzundern wird die Oberfläche des Metalls gereinigt und für weitere Bearbeitungen vorbereitet. Zusätzlich kann es beim Brennschneiden vorkommen, dass scharfe Kanten oder Grate entstehen, insbesondere an den Rändern des geschnittenen Metallstücks. Das Entgraten ist der Prozess, bei dem diese scharfen Kanten oder Grate entfernt werden, um eine glatte und saubere Oberfläche zu erzielen. Dieser Schritt ist wichtig, um Verletzungen zu vermeiden und um sicherzustellen, dass das Werkstück die erforderlichen Maße und Oberflächeneigenschaften hat.
Für die weitere Veredelung bieten wir Ihnen die Möglichkeit die Brennteile zu Entzundern und zu Entgraten. Dabei entfernen wir nicht nur die prozessbedingte Brennschlacke an der Unterseite der Brennzuschnitte sondern die Kanten können gebrochen oder verrundet werden, die Fläche des Brennschnitts kann verschliffen werden oder die Bauteile können auf unserer Entzunderungsanlage gestrahlt werden. Erfahren Sie mehr über Ihre Möglichkeiten hier: Entzundern und Entgraten
Fasen der Zuschnitte
Das Fasen bezeichnet das Anbringen einer Abschrägung oder Kante an einem Brennteil oder Werkstück. Diese Technik wird oft angewandt, um Vorbereitungen für Schweißnähte zu treffen, indem man die Kanten des Brenteils abschrägt, um eine optimale Schweißfuge zu erzeugen. Fasen können in verschiedenen Winkeln ausgeführt werden, je nachdem, welche Art von Schweißnaht erforderlich ist.
Das Fasen beim Brennschneiden verbessert nicht nur die Qualität der Schweißverbindung durch die Schaffung einer größeren Oberfläche für das Schweißmaterial, sondern kann auch dazu beitragen, die Spannungen im Material zu reduzieren, die durch den Schweißprozess entstehen können. Um Ihnen in der Weiterverarbeitung saubere Schweißnähte zu ermöglichen, bieten wir Ihnen das präzise Fasen der Brennkante mittels CNC-gesteuerter Fasenroboter an. Damit erfüllen wir auch die anspruchsvollsten Vorgaben unserer Kunden. Weitere Informationen zur perfekten Schweißnahtvorbereitung erfahren Sie hier: Fasen
Gerne erörtern wir mit Ihnen gemeinsam, welches Fertigungsverfahren, welche Toleranzklassen und welche weiteren Zusatzarbeiten für Ihren Anwendungsfälle das Optimum darstellen. Rufen Sie uns an oder senden Sie uns eine Mail.